Ball Nose End Mills vs Circle Segment Tools: A New Era In Machining
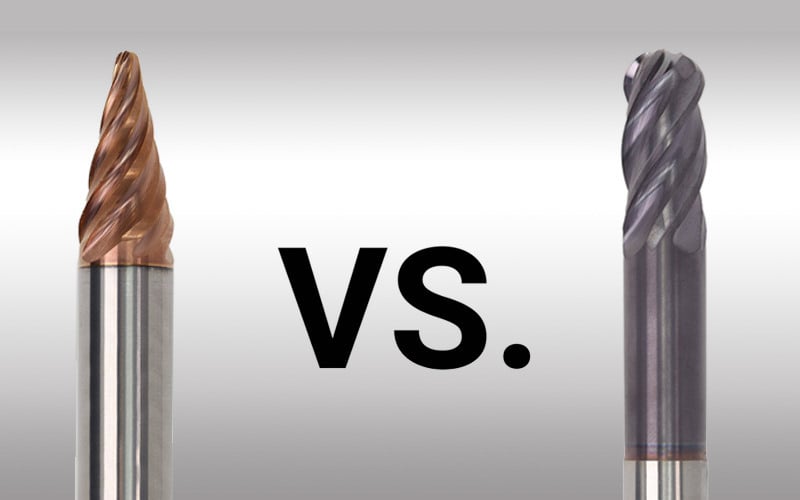
In the realm of precision machining, choosing the right cutting tool can significantly affect both efficiency and quality. For many years, ball nose end mills have been the standard choice for machinists, valued for their versatility and dependability. However, recent advancements in cutting tool technology have introduced a new class of tools known as circle segment end mills. This article compares the characteristics of ball nose end mills and circle segment tools, examining their capabilities, the machines they require, and the industries that benefit most from circle segment tools.
The Ball Nose End Mill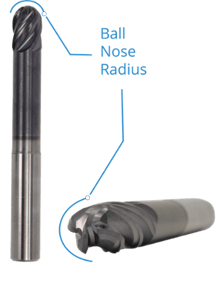
The ball nose end mill is a staple in machining. Its simple design, with a rounded tip, allows for smooth contouring and profiling on a variety of workpiece surfaces. This tool has been widely embraced due to its ease of use and its consistent circular profile maintenance. However, it has its limitations.
One of the main drawbacks of the ball nose end mill is the extended cycle time required to achieve a smooth surface. To get the desired finish, a small step over increment is needed, leading to lengthy machining cycles, especially on large surfaces. This limitation has driven machinists to explore alternatives that can enhance both efficiency and precision.
Circle Segment Tools: A Superior Alternative?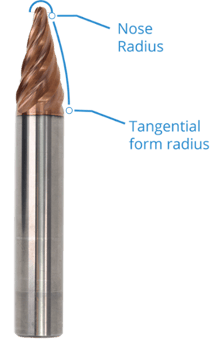
Circle segment end mills present a compelling alternative to ball nose end mills for many mealworking applications. These tools feature a unique geometry that enables efficient finishing and semi-finishing profiling operations. The key advantage of circle segment tools lies in their ability to significantly reduce finish-milling times while improving surface finishes, making them ideal for complex-contour workpieces.
When used on 5-axis CNC machines, circle segment tools unleash their full potential, maximizing productivity gains. However, they require advanced software and specialized training. On the other hand, 3-axis machines, while more accessible, do not fully utilize the tool’s capabilities and require less sophisticated software and training. Although manufacturers may initially save on costs by choosing 3-axis machines, they could miss out on substantial cycle time reductions that could quickly justify the investment in circle segment tools.
Features and Benefits of Circle Segment Tools
Circle segment tools offer numerous advantages, including:
- Efficiency in Finishing: These tools excel in finishing and semi-finishing profiling operations, allowing you to significantly reduce cycle times. Their large-radius cutting edges allow for much larger step overs, leading to up to 90% faster task completion.
- Deep Cavity Machining: Circle segment tools are versatile, making them ideal for machining deep pockets and hard-to-reach areas without the need for long-reach tools. This versatility simplifies the machining of profiles and blends.
- Enhanced Surface Quality: Circle segment tools provide the same theoretical scallop height while allowing for a greater axial depth of cut, improving efficiency and surface finish. Depending on the step over strategy and the tool’s geometry, circle segment tools can achieve lower cusp heights compared to ball nose end mills, resulting in smoother and more precise surface finishes.
- Longer Tool Life: The unique geometry of circle segment tools reduces cycle time, leading to less wear and a longer tool life.
- Reduced Post-Machining Processes: Circle segment tools can reduce or even eliminate the need for time-consuming post-machining processes such as finishing and polishing, saving both time and resources.
Special Features of SGS Circle Segment Tools
While all circle segment tools offer remarkable benefits, SGS’s line of circle segment end mills takes these advantages even further with additional features:
- Variable Geometry: SGS’s circle segment tools include variable geometry designs that reduce chatter, extending tool life and ensuring consistent performance even in demanding machining applications.
- Wear-Resistant Coatings: Equipped with proprietary coatings, these tools offer extreme wear resistance, enhancing durability and minimizing the need for frequent replacements.
- Wear-Resistant Substrate: SGS tools feature hard micro-grain substrates and are subject to rigorous quality control, resulting in extreme wear resistance and superior performance.
Industries That Benefit From Circle Segment Tools
Circle segment tools are particularly advantageous in industries that require precision, efficiency, and the machining of contoured workpiece surfaces. The use of circle segment tools most benefits industries that demand superior precision, including:
- Medical: For applications like femoral knees and trauma plates, where precision is crucial.
- Aerospace: Ideal for machining blisks, discs, and blades with complex geometries.
- Power Generation: Perfect for turbine blades and impellers.
- Mold and Die: Well-suited for deep cavities and intricate mold machining.
- Automotive: Used for machining complex shapes and profiles.
a new era of precision machining
Circle segment end mills are revolutionizing the industry by significantly reducing cycle times, improving surface quality, and extending tool life. Kyocera SGS provides a comprehensive range of tools featuring variable geometry for chatter reduction, wear-resistant coatings, precise form tolerance, and a wide variety of sizes to suit specific applications. SGS’s Circle Segment tools are designed to deliver optimal performance and help you achieve unmatched efficiency and quality in your machining operations. Contact the A&M Industrial Metalworking Team to learn how you can upgrade your tooling and elevate your machining capabilities with SGS circle segment tools.