Tungaloy Wear Problems And Solutions Chart For Carbide Inserts
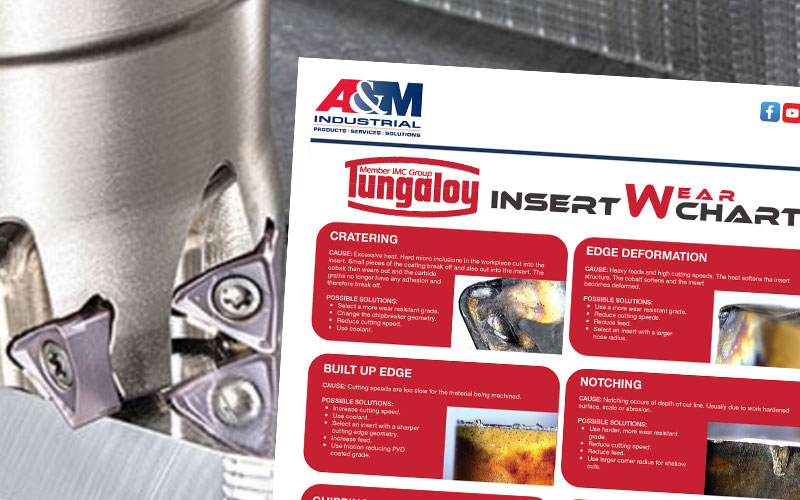
Learn the cause and solution to the most common insert wear problems. Utilize the Tungaloy Insert Wear Chart to quickly identify the root cause of carbide insert wear problems including built up edge, chipping, cratering, edge deformation, flank wear, notching, and thermal cracking. Utilize the expert recommendations provided to fix the issue and optimize your machining process. Learn how to tackle the most common insert wear problems and keep your Tungaloy inserts performing at their best.
PROBLEM | CAUSE | POSSIBLE SOLUTION |
BUILT UP EDGE |
Excessive heat. Hard micro inclusions in the workpiece cut into the insert. Small pieces of the coating break off and also cut into the insert. The cobalt then wears out and the carbide grains no longer have any adhesion and therefore break off. |
To avoid built up edge on your inserts, the following is recommended: Select a more wear resistant grade. |
CHIPPING |
Chipping is caused when the insert grade is too hard for application conditions. |
To avoid chipping your inserts, the following is recommended: Use a tougher grade with higher cobalt content. |
CRATERING
|
Insert cratering is caused by excessive heat. In addition, cratering can occur when hard micro inclusions in the workpiece cut into the insert. Also, small pieces of the coating can break off and cut into the insert. The cobalt then wears out and the carbide grains no longer have any adhesion, and therefore break off. |
To avoid cratering on your inserts, the following is recommended: Select a more wear resistant grade. Change the chipbreaker geometry. Reduce cutting speed. Use coolant. |
EDGE DEFORMATION |
Heavy feeds and high cutting speeds can cause edge deformation. The heat softens the insert structure, causing the cobalt to soften and the insert becomes deformed. |
To avoid deforming the edges of your inserts, the following is recommended: Use a more wear resistant grade. |
FLANK WEAR |
Flank wear occurs when the insert grade is too soft and machine speed is too fast. |
To avoid flank on your inserts, the following is recommended: Reduce cutting speed. |
NOTCHING |
Notching occurs on an insert at the depth of cut line. This is usually due to work hardened surface, scale or abrasion. |
To avoid notching on your inserts, the following is recommended: Use harder, more wear resistant grade. |
THERMAL CRACKING |
Rapid change in thermal loads can cause thermal cracking. Temperature difference between warm and cold zones causes thermal stress which leads to cracking of the insert. |
To avoid thermal cracking on your inserts, the following is recommended: Use heat resistant grades. |
Watch The Latest TunGaloy Videos
See Tungaloy's latest innovations in action, including the Tungaloy AddForce line! A&M Industrial's YouTube channel features hundreds of application videos and product introductions, plus exclusive videos you can only watch at A&M!