Essential Precision Measuring Equipment For Machinists
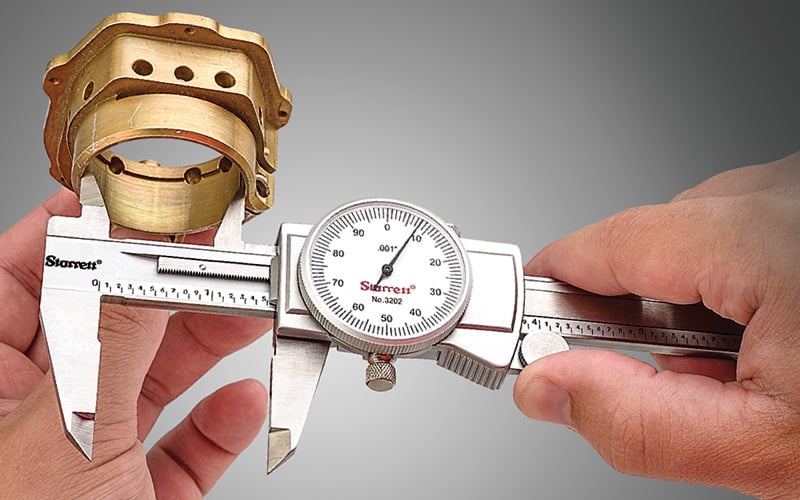
Precision is the heart of machining. Discover the five essential precision measuring tools every machinist needs to deliver impeccable accuracy and craftsmanship. These five precision measuring tools are a must-have for any professional machinist, essential for elevating the precision and quality of your work.
The Essential Role of Precision in Machining
In the world of industrial manufacturing, precision is not just a requirement; it's a necessity. Accurate measurements ensure that components fit together perfectly, machinery operates smoothly, and products meet stringent quality standards. This level of precision is what separates top-tier machinists from the rest.
Every machinist knows that even the smallest deviation can result in significant issues down the line. That's why investing in high-quality precision measuring tools is crucial. These tools are the backbone of any machining operation, providing the accuracy needed to maintain the integrity of the work.
Micrometers: The Backbone of Precision Measurement
Micrometers are essential tools in a machinist's arsenal. They offer unparalleled accuracy for measuring small dimensions, typically within the range of a few inches or millimeters. Available in various forms, such as outside micrometers, inside micrometers, and depth micrometers, these instruments are designed for specific measurement tasks.
Outside micrometers are commonly used for measuring the thickness and outside diameters of objects, while inside micrometers measure the internal dimensions of holes and slots. Depth micrometers, on the other hand, are used to measure the depth of holes and recesses. Regardless of their type, micrometers provide the precision needed for detailed and intricate work.
Calipers: Versatility Meets Accuracy
Calipers are known for their versatility and are a staple in any machinist's toolkit. These tools can measure both internal and external dimensions, as well as depths. There are several types of calipers, including vernier calipers, dial calipers, and digital calipers, each offering different levels of ease and precision.
Vernier calipers are traditional and require manual reading, while dial calipers provide a dial readout for easier measurements. Digital calipers, the most advanced, offer digital readouts and are often equipped with additional features such as data output for recording measurements. Regardless of the type, calipers are indispensable for quick and reliable measurements.
Dial Indicators: Ensuring Perfect Alignment
Dial indicators are critical for ensuring that machinery and components are perfectly aligned. These tools measure small distances and angles with high precision, making them ideal for setup and inspection tasks. They are commonly used in conjunction with other tools, such as surface plates and height gauges, to check the flatness, straightness, and alignment of surfaces.
The dial indicator's easy-to-read face and intuitive operation make it a favorite among machinists. Whether you're aligning a machine part or checking for runout, a dial indicator provides the accuracy and reliability needed to ensure that everything is in its proper place.
Gage Blocks: The Standard of Calibration
Gage blocks are the gold standard for precision measurement and calibration. Gage blocks and gage block sets are used to calibrate other measuring instruments, ensuring their accuracy over time. Made from high-quality steel or ceramic, gage blocks are available in gage block sets of varying sizes and combinations.
Each block's thickness is meticulously manufactured to exact standards, allowing machinists to build up accurate lengths by stacking them. This modularity makes gage blocks incredibly versatile and invaluable for maintaining the precision of other tools, such as micrometers and calipers. In any machining environment, gage blocks are essential for achieving and maintaining the highest level of measurement accuracy.
Surface Plates: An Essential Flat Reference
A surface plate is an essential precision measuring tool that every machinist should own because it provides a stable, flat reference surface critical for accurate inspection, layout, and measurement tasks. Most often made of granite, a surface plate resists warping and wear, ensuring long-term dimensional stability. Machinists rely on surface plates to perform high-precision measurements with tools like height gauges, dial and test indicators, and angle blocks, allowing for consistent results in flatness inspection, part alignment, and dimensional verification. Whether you’re checking part tolerances, squareness, or surface flatness, a quality surface plate is the foundation of any high-accuracy machining workflow.
Starrett Precision Measuring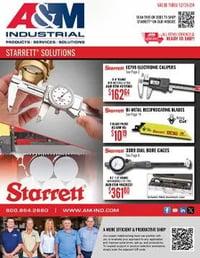
For a limited time only, save on select Starrett Precision Measuring Essentials, including Starrett Calipers, Starrett Micrometers, Starrett Measuring Sets and more. For assistance with selecting the right precision measuring tools for your application, contact the A&M Industrial Metalworking Team.