How To Avoid Arc Flash: 7 Steps To Avoiding Electrical Hazards
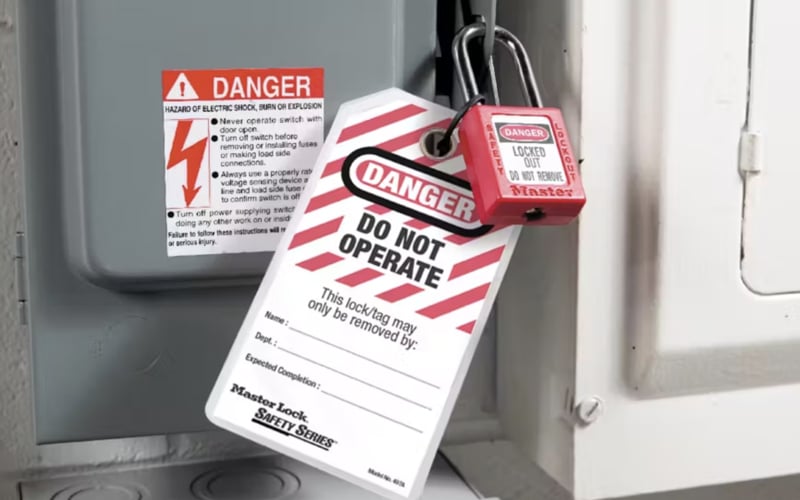
Every day, an estimated five to 10 arc flash incidents occur and more than 2,000 people are hospitalized each year, according to The National Fire Protection Association (NFPA).
With arc flash and other electrical hazards posing dangerous risks to employees, it’s vital to have strong electrical safety policies in place before these types of incidents happen. For safety professionals who are not sure if their facilities are fully compliant or looking to strengthen their existing electrical safety practices, the following checklist can provide a useful starting point.
1. Assess All Potential Risks and Develop Your Electrical Safety Policy
A documented electrical safety policy provides the foundation for protecting employees involved in maintaining the electrical distribution system and the equipment that runs on it. Begin building the policy with a comprehensive understanding of the tasks your employees must perform and the risks associated. A risk assessment of each task must be performed and documented, as noted in NFPA 70E 110.1(H), to capture details on the employee’s exposure to electrical hazards, the associated risks, and the implementation of controls.
In addition to the documented risk assessments, round out the electrical safety policy with the following:
- Specifications, drawings, and test reports related to the electrical system and the equipment within it. Documented results from IR scans and the arc flash risk assessment are needed to meet OSHA, NFPA 70E, and insurance requirements. The policy should also identify the person(s) responsible for maintaining this documentation.
- Job planning and access to the proper tools and equipment supplied by the organization to the qualified employee.
- Safe work practices and PPE requirements based on task and incident energy exposure.
- Preventative and predictive maintenance strategies to limit or mitigate the need to enter an electrical panel.
- Documentation of all inspection results, studies, trainings, hazard analyses, etc. related to a company’s electrical safety system. This helps validate that the requirements outlined in the electrical safety policy are consistently being followed and that there’s written record of it.
- Recorded results from electrical safety program audits, which should be completed every three years and capture any changes to equipment, processes, or people.
- Training programs (type of training, who will receive it, at what intervals should the training be administered, etc.).
2. Qualified Workers Tasks and Third-Party Resources
Once all of the electrical tasks and activities have been documented, it is crucial to put them through a risk assessment procedure or hazard analysis. Tasks that are frequently performed by company employees should have a level of risk acceptable to the organization. However, tasks with high risk, such as racking a breaker panel or when dealing with high voltage systems, are recommended to be outsourced if they fall outside of the experience and knowledge of a company’s qualified workers.
The output of this process will be invaluable when understanding how to structure your electrical safety management system, as well as how to define the roles and responsibilities of your internal qualified workers. This is the foundation of your electrical safety policy and will cascade to the rest of the activities your organization must complete to comply with OSHA and NFPA 70E Standards.
3. Evaluate Your Training Programs
After the process to determine which tasks a qualified worker will perform comes the evaluation of the type of training they will need. Each qualified worker must complete the NFPA 70E Compliance Training Course to perform any electrical tasks. This course must be taken every three years, unless inspections, behaviors, changes in equipment and technology, or changes in job duties require it to be more frequent.
Per NFPA 70E 110.2(4): training “…shall be classroom, on-the-job, or a combination of the two. The type and extent of the training provided shall be determined by the risk to the employee.” In addition to the NFPA standard, OSHA CFR 1910.332 outlines training requirements for electrical work activities and includes skills and techniques to “distinguish exposed live parts from other parts of electric equipment,” and the ability to “determine the nominal voltage of the exposed live parts.” As the organization is determining risk it is important to understand that all qualified employees are not alike. There are differences in knowledge, skill, and experience and that determines the level, content, and nature of the training required for each individual.
As a best practice, consider implementing an internal program for qualified workers that not only includes classroom training, but also hands-on training of the qualified worker’s specific tasks. The training program can be tailored to the individual based on their abilities and the risks associated with the electrical tasks. Every year, employers must evaluate their employee training and make sure it is current to NFPA requirements.
4. Arc Flash Risk Assessment
The arc flash risk assessment determines the level of incident energy within an electrical device and communicates through the arc flash warning labels how a qualified worker should engage the equipment, including approach boundaries and personal protection equipment (PPE) for arc flash and shock protection.
A Comprehensive Arc Flash risk assessment will include the following:
- One-Line Diagram outlining the power distribution throughout your facility. A current one-line diagram accurately describes the power system and provides the foundation for the risk assessment.
- Short Circuit Study determining if your equipment is properly rated to withstand a short circuit current.
- Device Interrupt Rating and Evaluation determining if protective devices have adequate interrupting capacity for the available short circuit current and verifying that electrical equipment is rated to safely handle short circuit currents without creating hazardous conditions.
- Protective Device Coordination Study determining “total clearing time” at fault currents and probable sequence of which device will open during a fault.
- Arc Flash / Incident Energy Analysis calculating the incident energy and arc flash boundaries which, in turn, determines the specific arc-rated clothing and minimum PPE requirements.
- Written Analysis providing the formal documentation of the arc flash study and including recommendations for mitigating the potential for arc flash.
Should companies feel the need to consult a trusted third-party partner, A&M Industrial Safety Services offers decades of dedicated safety experience and training to ensure that your organization’s needs are met. With an A&M Industrial's Arc Flash Risk Assessment, businesses of all sizes can achieve the following:
- Adherence to current NFPA 70E standards (2021)
- On site data collection by service technicians
- Utilization of licensed professional engineers experienced in power systems studies to accurately model the system and conduct the arc flash study
- Comprehensive deliverables including the documented results from the arc flash study, recommendations on mitigation, and the application of the arc flash labels to the equipment
5. Label Requirements
Once the arc flash risk assessment is complete, the warning labels are applied to the electrical equipment. The information on the labels should include the following:
Nominal System Voltage- Arc Flash Boundary – i.e. the approach limit from an arc source at which incident energy equals 1.2 cal/cm2
- Available Incident Energy and Corresponding working distance, or Arc Flash PPE category from Table 130.7 (C)(15)(A), but not both.
- Minimum arc rating of clothing
- Specific level of PPE
6. Determine What PPE Will Best Protect Your Employees
There are two approaches to selecting the appropriate personal protection equipment. The first and recommended approach is to utilize the incident energy analysis from the arc flash risk assessment.
An alternate approach, called the Table Method, utilizes NFPA 130.7(C)(15)(a) Arc-Flash PPE Categories for Alternating Current Systems and 130.7(C)(15)(b) Arc-Flash PPE Categories for Direct Current Systems. This table provides the category of PPE based on the nature of the task and voltage of the equipment on which the task is being performed.
The table method, however, is not as precise as an incident energy analysis since the specific incident energy of the electrical equipment is not known. Assigning arc-rated clothing and accompanying PPE commensurate with the results of the incident energy analysis is highly recommended.
7. Maintain A Strong Safety Culture with Routine Assessments
An arc flash risk assessment should be conducted every five years. If updates to the electrical system are made or equipment is added, an arc flash risk assessment should be performed upon completion of those changes. By performing a risk assessment every five years, organizations can ensure that revisions to the NFPA 70E® or NEC (National Electric Code) standards – which occur every three years – are captured and incorporated into the assessment.
Checklist Summary
Electricity is a very unpredictable type of energy, making it critical for your company to have robust electrical safety protocol and policies in place. Companies without a thoroughly vetted electrical safety policy can put their employees at extreme risks like arc flash if engaged in tasks that put them close to energized systems. The comprehensive nature of the requirements to evaluate, assess, document, train, communicate, review, and audit is intended to reduce and eliminate the likelihood of shock and arc flash. By following these steps, you can not only invest in the safety and well-being of your employees, but also improve the efficiency of your facility’s operations and ultimately, your bottom line.
To learn more about creating, auditing, or updating your electrical safety programs, visit Master Lock’s Arc Flash & Electrical Safety website or contact the A&M Industrial Safety Team via the form below to request an Arc Flash Risk Assessment.
A&M Industrial Safety Services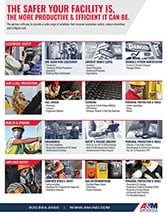
The A&M Industrial team of safety experts can partner with you to evaluate the safety of your facility and to perform over a dozen services, including Arc Flash Risk Assessment and Logout Tagout. To learn more or to request a safety service, visit the safety page on our website or download our safety services listing and brochure using the button below.