How To Choose The Right Cutting Wheel For Your Angle Grinder
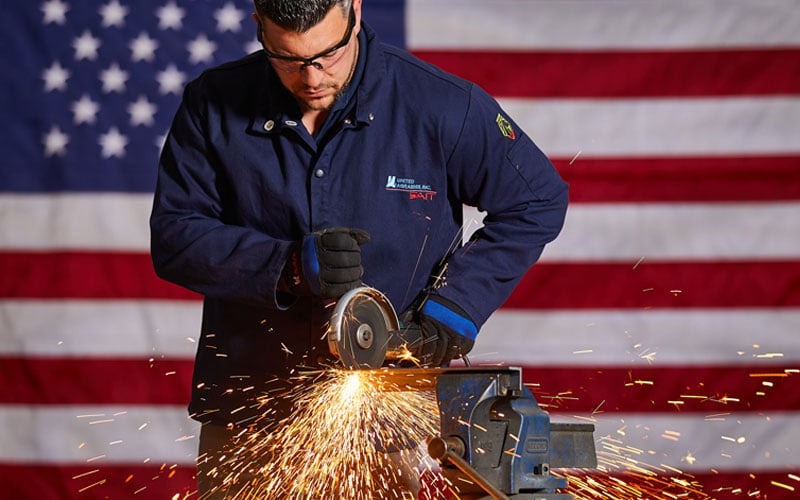
With so many cutting wheels available, choosing the right cutting wheel for your angle grinder, and for cutting the material you’re working with, can be a challenge. In this article, we’ll review the characteristics of a cutting wheel to consider when you choose a cutting wheel for your application.
What is A Cutting Wheel?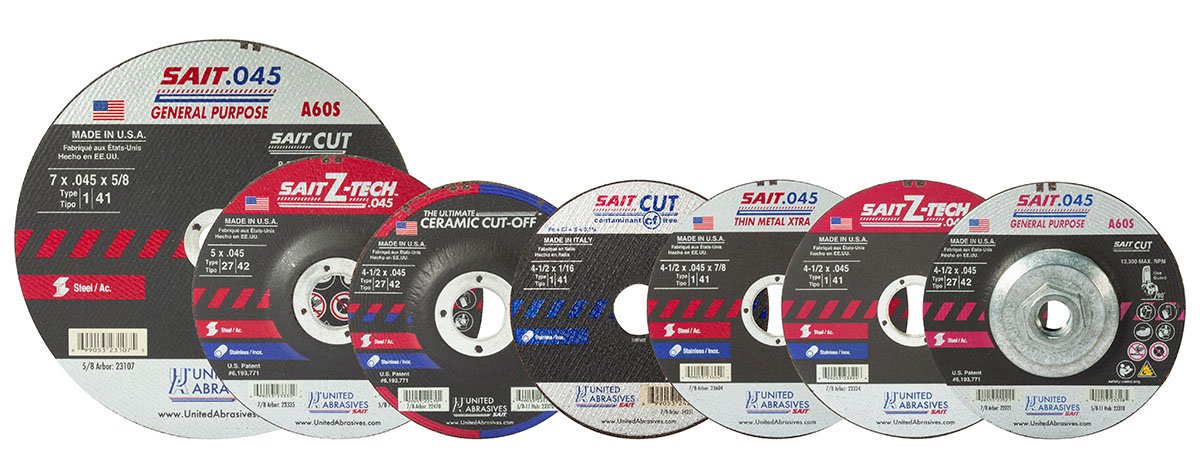
Cutting wheels, also known as cut-off wheels, typically make narrow, precise cuts into a material at 90° angles. Cutting wheels cut into a material, as opposed to abrasive grinding wheels that grind large pieces of material off a workpiece from a shallow angle. Cutting wheels differ from grinding wheels in both their function and their structure. The largest advantage to using a cutting wheel and angle grinder is that they are easily configured to cut when needed.
Which Cutting Wheel, when?
.045 cutting wheels are designed specifically for cutting metal and have a much thinner thickness (known as “Kerf”) than grinding wheels (1/4”) and pipeline wheels (1/8”). This is because grinding and pipeline wheels are designed primarily for grinding metal as opposed to cutting. The added thickness of a grinding wheel makes it difficult for cutting jobs, as the user would need to remove more material in a cut, leading to frustration and a longer, less efficient cutting time.
- .045 Wheels: United Abrasives .045 wheels are the best choice for efficient cutting. Note that .045 wheels should never be used for deburring metal after cutting or grinding, as this type of misuse could result in wheel failure and in severe injury.
- .090 Wheels: United Abrasives .090 wheels are designed for cutting and notching metal. Notching is a shearing process during which a metal scrap piece is removed from the outside edge of a metal workpiece prior to welding.
- .095 Ultimate Combo Wheels: United Abrasives most versatile cutting wheel is the Ultimate ComboWheel, featuring a .095 thickness. This unique thickness of this abrasive wheel allows operators to cut, notch, deburr, and light grind without the need to change the wheel.
types of Cutting Wheels
There are two basic configurations of cutting wheels:
- Type 1 / Type 41: This is a flat cutting wheel that allows for a maximum depth of cut. The main disadvantage of using a Type 1 wheel is that they mount closer to the guard making it more difficult for the user to see what they are cutting.
- Type 27 / Type 42: Originally developed and patented by United Abrasives, this design features more of a rigid feel while cutting, enhanced operator visibility of the cut, and the ability to flush cut (as the raised hub allows for the locking nut to be recessed). These cutting wheels are also available from United Abrasives with a 5/8-11 quick change hub for ease of mounting.
Abrasive Grains
Abrasive grains are hard, sharp materials that can be used to wear away another material when one or the other is moved in pressurized contact. The most widely used abrasive grains include:
Aluminum Oxide: the most common and popular abrasive used in grinding wheels, aluminum oxide is the grain of choice for grinding high speed steel, carbon steel, alloy steel, annealed malleable iron, wrought iron, bronze and most metals. Aluminum oxide typically has a lower initial cost for the user, and delivers very good cut rates and reliable durability. Within the United Abrasive product line, the A60S and A46N feature aluminum oxide grain.
Ceramic Aluminum Oxide (Alumina Ceramic): this industrial synthetic grain fractures at a controlled rate at the submicron level, constantly creating thousands of new cutting points. Exceptionally strong, ceramic aluminum oxide is primarily used for precision grinding and high performance applications on steels, alloys, and hard-to-grind materials. Ceramics also tend to cut cooler, minimizing discoloration while maximizing product life. Within the United Abrasive product line, the SAITECH and the Ultimate Ceramic cutting wheels both feature ceramic grain technology.
Zirconium (also known as Zirconia Alumina or Zirc): made from a mixture of both aluminum oxide and zirconium oxide, this tough abrasive grain works well in high performance grinding applications, including cut-off operations, on a broad range of steels and steel alloys. Zirconium grain has an extremely durable design that allows long life and a low cost-per-cut ratio. Within the United Abrasive product line, the Z-Tech cutting wheels feature zirconium.
So, What Cutting Wheel do i use?
Ultimately, the right choice of cutting wheel to use with your angle grinder depends on what you’re cutting and your preferences. Use the United Abrasives chart below to help you determine the appropriate wheel.
Need More help selecting the right Cutting Wheel?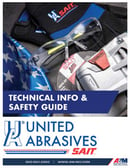
Download the United Abrasive Technical Info & Safety Guide for comprehensive selection charts and technical data on their wide offering of cutting wheels, flap discs, grinding wheels and more.