How To Measure & Improve Cutting Fluid Performance
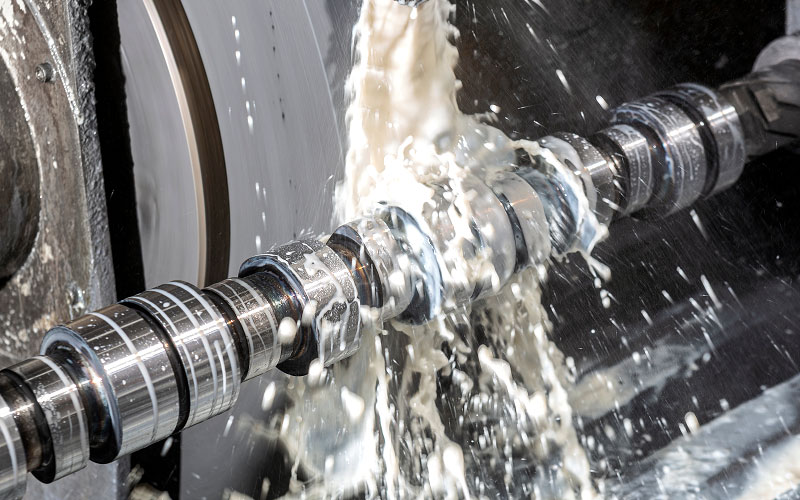
The performance of your shop's cutting fluid, and how well your cutting fluid is maintained, has a significant impact on your overall operating costs. Use of a low-quality metalworking fluid, use of the wrong metalworking fluid for your application, or poor maintenance of your cutting fluids, can slow down productivity, lead to waste, and cause downtime that inevitably drives up operating costs.
Meanwhile, use of high-quality, well-maintained coolant and metalworking fluids provides a higher return on investment, reduces downtime, and provides cost savings. In order to gauge how efficiently your shop is utilizing cutting fluids, you have to track your cutting fluid performance and the impact it is having on your budget.
How to Track Cutting Fluid Performance
To measure your shop’s cutting fluid performance, you need to create a tracking system and perform fluid manufacturer-recommended procedures. It is important to know the different parameters to track and what you should be monitoring. The following indicators can help you better analyze your shop's cutting fluid usage and efficiency:
Sump life
Make sure you’re practicing proper coolant maintenance to maximize the life of your metalworking fluids and measuring how long your fluids lasts in the sump before they require replacement. Performing regular fluid maintenance and upgrading to a more advanced coolant will extend sump life and provide a higher return on investment. With cutting fluids, as with anything else, you do truly get what you pay for – generally, more advanced coolants outperform their less expensive counterparts.
Tool life
Your metalworking fluids serve as the lifeline of your shop. High-performance cutting fluid provides better lubrication and cooling, reducing wear on a cutting tool's cutting edges, thus extending tool life. Tool life serves as a valuable measure of how effective a cutting fluid is at providing protection during a machining operation.
Makeup rate
If an operation requires high concentrations and frequent cutting fluid top-ups, that could indicate a problem with carry off, evaporation, or foam — issues that can be solved by upgrading to more advanced cutting fluid and more efficient coolant makeup systems. The downtime experienced while performing frequent fluid changes can be eliminated and your shop's efficiency can benefit from the use of advanced metalworking fluids.
Coolant disposal rate
Another way to spot problems with carry off or a short sump life, high fluid disposal costs draw attention to how much coolant you’re replacing. This can indicate your shop would likely benefit from use of a more advanced cutting fluid, and also may indicate your fluid maintenance may require further review to ensure you are following manufacturer-recommended usage and ratios/maintenance procedures.
Throughput
High-performance cutting fluid allows operators to run machines at higher speeds without sacrificing quality or damaging machinery or equipment. Advanced cutting fluids have been shown to more than double throughput in some operations.
Finish quality
Poor finish quality requires additional reworking, which decreases throughput. This is often an indicator of insufficient lubrication and cooling from the cutting fluid and can be a leading indicator of poor tool life.
WASTE / Scrap rate
A high scrap rate is especially costly because it results in direct loss of materials, which directly impacts your bottom line.
Clean outs per year & Required DOwntime
More frequent clean outs result in higher consumption rates and more machine downtime.
Tracking machine downtime also helps track the total lost productivity due to fluid and cutting tool change outs, sump clean outs, and machine cleaning and maintenance.
reviewing your facility's cutting fluid performance
You've tracked the aforementioned performance indicators, now what? Over the course of as little as a month, you can establish a clear benchmark of how your current cutting fluid is performing, as well as its impact on your operating budget. From there, you can set coolant cost-cutting goals and analyze the performance of an alternative cutting fluid using this same method. Once you have both sets of metrics, compare the numbers to determine which fluid provides better value overall.
In conclusion, measuring the performance of cutting fluids is essential to ensuring optimal cutting quality and tool life, and is also essential to managing your facility's operating costs. The metalworking experts at Master Fluid Solutions® and A&M Industrial can provide comprehensive audits to identify potential areas of improvement, and provide insight into how to streamline your facility's operations. Contact the A&M Metalworking Team to schedule a site visit or consultation, request metalworking fluid selection assistance, or fluid usage and maintenance recommendations. We carry a wide range of metalworking fluids by Master Fluid Solutions®, Rustlick, Blue Chip, and more.