How To Use A Refractometer: Manufacturing & Coolant Applications
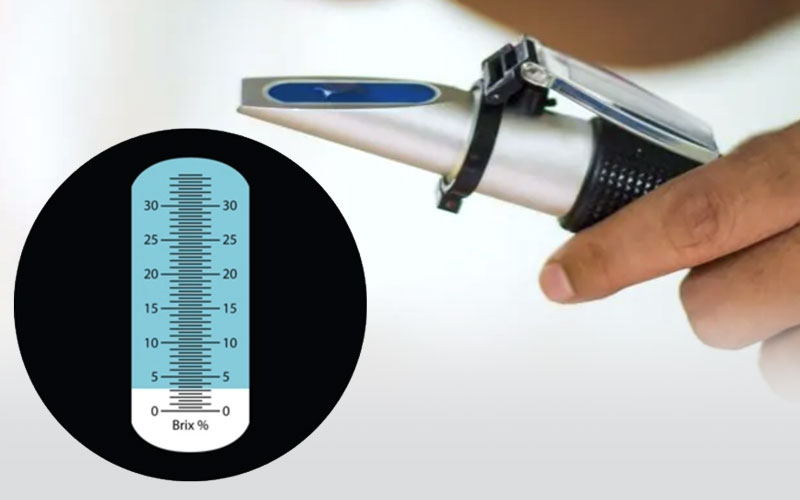
Discover the practical applications and usage of a refractometer in the manufacturing industry and learn how it can help optimize processes and improve productivity.
Understanding the Basics of a Refractometer
A refractometer is a precision measuring and testing instrument used to measure the refractive index of a substance. The refractive index is a measure of how light bends as it passes through a material. By measuring the refractive index, a refractometer can determine the concentration or purity of a liquid or solid sample. This makes it a valuable tool in the manufacturing industry, where maintaining the correct concentration of coolant, metalworking fluids, and sump is crucial for optimal performance.
To use a refractometer, first, ensure that it is in focus and properly calibrated. When focusing your refractometer, be sure the refractometer is creating a tight seal to your eye and allowing little to no light – this will help to increase the visibility of the scale and make focusing easier. Once the lines of the scale are crisp and defined, your refractometer is in focus. Calibrating your refractometer can be done using a calibration solution provided by the manufacturer. Once calibrated, the refractometer can be used to measure the refractive index of a sample. Simply place a few drops of the sample onto the prism surface of the refractometer and close the cover. Look through the eyepiece and adjust the focus until the boundary line between light and dark is sharp. Read the refractive index value from the scale provided.
Understanding the basics of a refractometer is essential for using it effectively in maintaining machining fluids and sump. It allows operators to accurately measure the concentration of coolant or cutting fluid, ensuring that it is within the recommended range. This helps prevent issues such as tool wear, poor surface finish, and inefficient machining.
Measuring Concentration and Purity with a Refractometer
One of the primary uses of a refractometer is to measure the concentration and purity of liquids. For example, in machining processes, coolant or cutting fluids need to have the right concentration to ensure optimal performance. By measuring the refractive index of the coolant, operators can determine its concentration and make adjustments as necessary.
To measure concentration, operators can use a refractometer along with a concentration chart provided by the coolant manufacturer. By comparing the refractive index reading with the chart, they can determine the concentration percentage. Similarly, in industries such as food and beverage, a refractometer can be used to measure the sugar content in various products, ensuring consistent quality and taste.
Measuring concentration and purity with a refractometer is a quick and accurate way to maintain machining fluids and sump. It allows operators to make informed decisions about the concentration levels, ensuring that the fluids are properly balanced for optimal performance.
TESTING COOLANT with a refractometer
Testing to ensure your coolants fall within manufacturer recommended constraints helps you to increase the efficiency and overall performance of the fluids, thus allowing a greater return on the investment you've made in your fluids and machinery. As coolants and machining fluids serve as the lifeblood of machine shops and manufacturing facilities, maintaining your fluids and sump allows for a more efficient, healthier and more productive shop. To test coolant with a refractometer, follow these steps:
- Extract coolant or fluid from your machine using a dropper.
- Place 2–3 drops of coolant onto the prism of the refractometer and secure its cover plate.
- Be sure there are no dry spots or air bubbles beneath the cover plate's surface, as this can effect your reading.
Read the scale value at the intersection of the dark and light portions, at the exact point where they meet on the scale. If necessary, adjust the position of the light source to maximize the contrast and allow better visibility of the shadow line. Optimal contrast can be obtained by holding the instrument underneath and perpendicular to a light source. Where that line falls on the scale equates to the concentration of your coolant.*
- Once you have completed your testing, be sure to wipe the lens dry with a clean cloth (do not wash or rinse) and place the instrument in the supplied case before storing in a dry environment.
Optimizing Industrial Processes with Refractometry
Refractometry plays a crucial role in optimizing various industrial processes. By using a refractometer, operators can monitor the concentration of fluids in real-time, allowing for timely adjustments and preventing issues such as tool wear, poor surface finish, and machine downtime.
In the metalworking industry, for example, maintaining the right concentration of coolant or cutting fluids is essential for efficient machining operations. A refractometer can help operators monitor the concentration levels and make adjustments as necessary, ensuring that the fluids provide adequate lubrication and cooling.
In addition to coolant monitoring, refractometry can also be used in other industries such as pharmaceuticals, chemical manufacturing, and automotive. It allows for precise control over the concentration of various substances, ensuring consistent quality and performance.
By optimizing industrial processes with refractometry, companies can improve productivity, reduce waste, and enhance product quality.
Ensuring Quality Control and Product Integrity
Maintaining product integrity and quality control is essential in various industries. A refractometer can be a valuable tool in ensuring that products meet the desired specifications.
In the beverage industry, for example, a refractometer can be used to measure the sugar content in juices and other beverages. This ensures that the products have the desired sweetness and taste. Similarly, in the pharmaceutical industry, refractometry can be used to measure the concentration of active ingredients in medications, ensuring that they are within the required range for effectiveness.
By using a refractometer for quality control, companies can minimize the risk of producing substandard products and ensure customer satisfaction. Similarly, verifying your coolants and machining fluids are at proper (manufacturer recommended) concentration levels ensures your fluids are providing optimal performance, protecting your machinery and tools, eliminating costly downtime, and providing a maximum return on your investment.
Coolant CoNcentration 101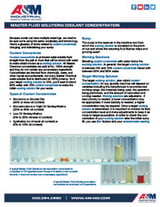
Utilize this handy downloadable reference for a coolant concentration glossary of terms, sump maintenance and coolant concentration recommendations, information on BRIX factors and refractive readings, and a Coolant Concentration Calculation Chart.