Most Common Coolant Problems & How To Fix Them
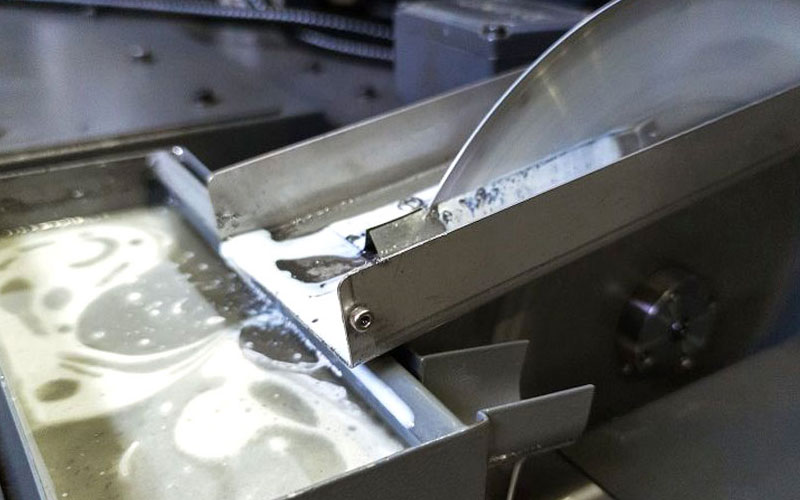
Coolant must be monitored and well-maintained to perform at its best. Even with premium products, coolant problems can occur due to a lack of coolant management, contamination, and water quality issues. These common coolant problems can shorten tool life, damage equipment, and can even cause rancid odors.
There are several ways to troubleshoot issues with your metalworking fluids and remedy common coolant problems, including:
Improperly mixed coolant
If your coolant isn’t mixed properly, it can negatively impact your coolant's performance. It’s important to note the proper concentration and to test the concentration regularly. You can measure the concentration with a refractometer or use the titration method. It is very important to know and understand your coolant’s refractometer (or Brix) multiplier for accurate concentration. The proper technique for mixing any of Master Fluid Solutions’ products is to add water first, then add the coolant concentrate, following the acronym OIL (oil in last). For the best coolant mixing results, we suggest an inline mixer.
Poor water quality
Along with proper coolant mixing and using the correct concentrations, it’s important to pay attention to the quality of the water used. In some cases, coolant can be 95%+ water. Hard water minerals in the water like calcium and magnesium can have detrimental effects on the emulsion quality of the fluid, leave residues, and provide food for bacteria. Additionally, sulfur and chlorine can wreak havoc on your coolant; these impair the fluid’s ability to provide adequate rust protection. Charging your coolant systems with reverse osmosis or deionized water can help avoid water-related coolant issues that negatively affect the fluid. The water should be analyzed by a coolant provider for proper recommendations.
Bacterial growth
Bacterial growth in the coolant can cause a host of problems, from releasing noxious gases in the air to causing corrosion. Starting with reverse osmosis or deionized water can help inhibit bacterial growth, as can regular machine maintenance and cleaning. Maintaining coolant pH and concentration control, and tramp oil removal are also critical. Preventative maintenance on tanks, pumps, chip conveyor, filter system, and plumbing will also help ensure the fluid is delivered properly and has less of a chance of contamination.
Tramp oil formation
Tramp oil forms when lubricating oil seeps into the coolant mixture. Tramp oil can enter and contaminate coolant from many sources, including machine seals, materials, tapping fluids, etc. It harms almost all coolants and can cause excess oil mist and smoke, and bacteria formation if it’s not removed. Tramp oil can be in three forms: free-floating, dispersed (temporarily mixed into the coolant by mechanical parts like pumps), or emulsified (bonded with the coolant).
To remove it, free-floating tramp oil can be skimmed off the surface with a belt or disc skimmer. Other efficient methods include absorbing it with an oil mat and removing it with a shop vacuum. Dispersed tramp oil can be coalesced or skimmed off the surface when the machine is idle. However, emulsified tramp oil can only be removed by centrifuge to avoid damaging the coolant. Using a machine cleaner such as Whamex causes free and dispersed oil to be emulsified, and it’s only used before a full system clean-out for an efficient and thorough machine cleaning.
Faulty filtration
During the metalworking process, metal fines are produced. If they’re not filtered properly, the coolant pumps can recycle them back into the cutting tool, which will reduce the life of the tools. Eventually, these small metal fines will form a dense sludge on the bottom of the coolant sump, which will encourage bacterial growth.
To prevent filtration issues, make sure the level of filtration matches the machining process and the desired surface finish.
Summary
The aforementioned common coolant problems are easily prevented with regular maintenance and proper fluid control. If you need help choosing the right coolant for your metalworking application, or assistance with diagnosing and treating a problem with your coolant, please contact the A&M Industrial Metalworking team.
Coolant CoNcentration 101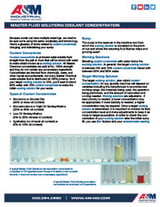
Utilize this handy downloadable reference for a coolant concentration glossary of terms, sump maintenance and coolant concentration recommendations, information on BRIX factors and refractive readings, and a Coolant Concentration Calculation Chart.