Metalworking Mistakes to Avoid: Enhance Your Metalworking Applications
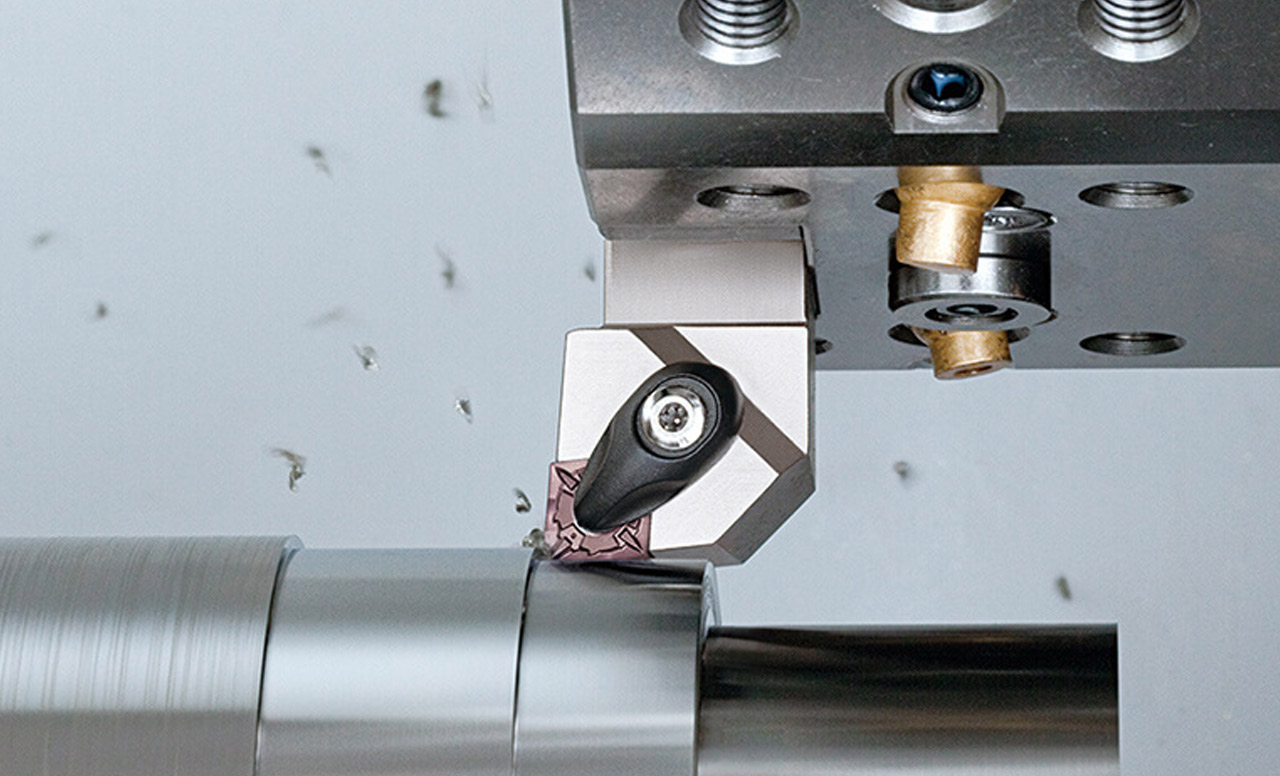
Metalworking is a complex and meticulous craft that requires attention to detail and skillful execution. While experience plays a significant role in mastering the art of metalworking, it's essential to be aware of common mistakes that can hinder progress and compromise the quality of your work. Let's explore some of the most common metalworking mistakes and provide insights on how to avoid them and enhance precision, efficiency, and overall craftsmanship.
1) Inadequate Planning and Design:
One of the most critical steps in metalworking applications is taking the time for proper planning and design. Failing to invest sufficient time in understanding project requirements and creating accurate blueprints can lead to costly errors. Before starting any metalworking project, take the time to plan meticulously, ensuring precise measurements, appropriate materials, and a clear understanding of the desired outcome. Contact the A&M Industrial Metalworking Team for tool and machinery selection assistance, speed and feed recommendations, and more. Utilize our Tap and Drill Size Chart, and Decimal Equivalent Chart to ensure you're utilizing the right tools for your metalworking applications.
2) Incorrect Material Selection:
Selecting the wrong type or grade of metal can have a significant impact on the final result. Each metal has unique properties, such as strength, corrosion resistance, and heat conductivity. Using an inappropriate material for the intended purpose can compromise structural integrity or lead to premature failure. Research and consult with experts to choose the right metal or raw materials for your specific project requirements.
3) Insufficient Safety Precautions: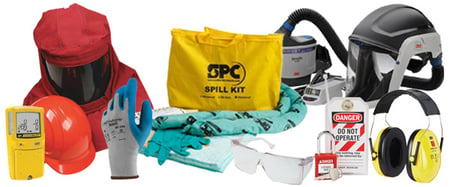
Working with metal involves inherent risks, including sharp edges, flying chips, and potential exposure to hazardous materials. Neglecting safety precautions can lead to accidents, injuries, or long-term health issues. Always wear appropriate personal protective equipment (PPE) including safety glasses, hearing protection, safety gloves, and respiratory protection when required, follow safety guidelines, and ensure proper ventilation in your workspace. Additionally, take regular breaks to avoid fatigue-induced mistakes.
4) Inadequate Tool Maintenance:
Metalworking tools, ranging from drill bits to pneumatic tools, require regular maintenance to perform optimally. Failing to clean, sharpen, oil, or replace worn-out tools can result in subpar results, increased cutting forces, and reduced efficiency. Implement a routine maintenance schedule, including sharpening, lubrication, and calibration, to ensure your tools are in top condition. Blue Chip brand G10 cleaners and degreasers, and wipers, offer a cost-efficient means to keep your tools and facility well maintained.
5) Poor Clamping Techniques:
Proper clamping is crucial for securing workpieces during metalworking operations. Inadequate clamping can lead to movement or vibration, resulting in inaccurate cuts, compromised precision, and even damage to the workpiece or equipment. Take the time to understand the appropriate clamping techniques for your specific project and ensure a secure and stable setup.
6) Neglecting Heat Management:
Heat management is essential in metalworking processes such as welding and heat treatment. Insufficient heat control can lead to distortion, warping, or even metallurgical issues. Proper preheating, post-heating, and temperature monitoring are essential to ensure controlled heat input and prevent unwanted effects on the metal's properties.
7) Lack of Documentation and Record-Keeping:
Maintaining accurate documentation and records throughout the metalworking process is often overlooked but can be highly beneficial. Documenting the materials used, process parameters, measurements, and any modifications made allows for better traceability, troubleshooting, and replication of successful outcomes. Keep a detailed log of each project to learn from past experiences and continuously improve your metalworking skills.
8) Inadequate Measuring:
Metalworking applications require precision measurements to ensure your parts are made to exacting specs. Utilize precision calipers, micrometers, indicators and more to verify accuracy. The saying 'measure twice, cut once' holds true in metalworking applications as well, and taking the time to ensure precision set-up, etc., results in final products that meet spec and reflect both professional craftsmanship and expertise.
9) Improper Material & Tool Storage:
It is crucial to maintain an adequate inventory of different materials to reduce lead times. However, it is important to consider the inherent properties of your raw materials when designing your storage area to prevent any damage. For instance, delicate materials that are prone to breakage should be stored in a secure area with minimal traffic. Additionally, it is advisable to store ferrous raw materials indoors and away from water and moisture to prevent corrosion. Any damage to the raw materials can result in defective final products or render the materials unsuitable for use. Similarly, care should be taken when storing delicate tools including precision measuring equipment which can rust. Taking precautions to protect and preserve the integrity of your materials and tools is essential to protecting their effectiveness and ensuring greater return on your investment.
10) Not keeping up with the times: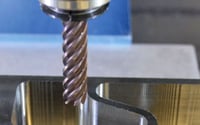
Staying at the cutting edge of innovation is critical to maintaining your competitiveness. New machinery, holemaking tools and milling tools, equipped with advanced geometries and coatings are constantly being introduced and contribute to greater efficiency and productivity. Utilizing new technology can increase your production capacity, help you maintain high quality standards, and often allows you to more efficiently manufacture a larger volume of parts for your customers. This enables you to offer cost savings to your customers, ensuring their satisfaction and giving you a competitive edge.
Conclusion
Metalworking is a blend of artistry, precision, and technical skill. By avoiding common mistakes, you can enhance the quality, efficiency, and overall success of your metalworking applications. Continuously educate yourself, seek guidance from experienced professionals including the A&M Industrial Metalworking Team, and embrace a mindset of continuous improvement. By doing so, you'll refine your craftsmanship and achieve remarkable metalworking results.