Increase Your Productivity: 5 Shop Productivity Roadblocks To Avoid
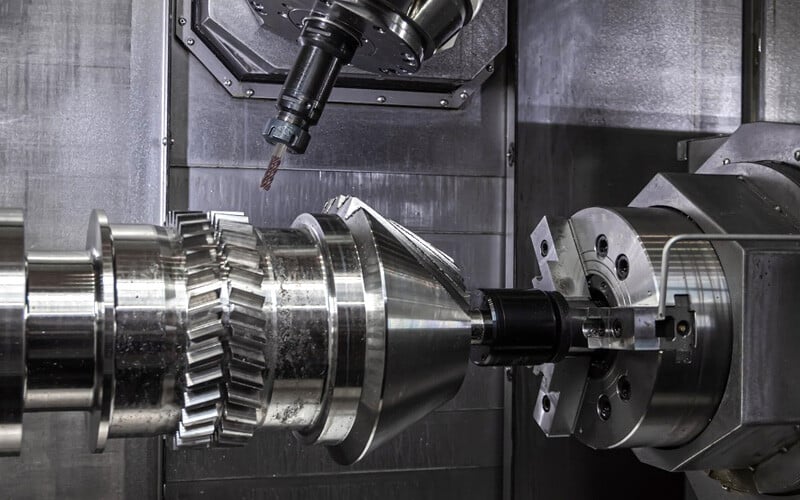
1. Selecting tools based on price
When combating the impact of inflation, reducing expenses might be a primary objective, but concentrating solely on minimizing initial costs (like tool prices) can ultimately be more expensive. The adage “It takes money to make money” holds some truth here. Running a successful manufacturing business requires savings derived from reducing cycle times, which enhances productivity and increases your bottom line. Using high performance cutting tools and larger or higher flute count tools (keeping in mind that adding flutes isn’t optimal for every application) will allow you to run the tools more aggressively and, when optimized, will be well worth the investment. This is especially true in high volume production settings and throughout high performance milling, threading, turning and metalworking applications.
2. Slowing tools down to extend tool life
While extending tool life is important, slowing down your tool to achieve this can severely hamper productivity. In low-volume runs, tool costs might seem more significant than in high-volume runs, but in both scenarios, tool life is not where profits are made. Profits come from optimizing parameters and reducing cycle times, which in turn increases throughput.It’s also worth noting that if the tool isn’t running fast enough, the coating may not be reaching its activation temperature, reducing the benefits of a coating. Contact the A&M Industrial Metalworking Team for help identifying how you can reduce cycle times and increase your productivity.
3. Using one tool path across the board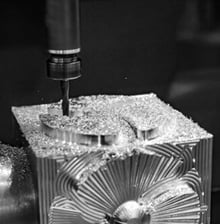
There is not a “one size fits all” tool path when it comes to productivity. Sure, you can use just about any tool path to machine a part, but some shops tend to become so laser focused on one, that they forget another tool path may better suit the application. The two main styles of tool paths are trochoidal, which is constant cutting engagement, and standard, which varies engagement angles. Since trochoidal is newer, some people think it is best, but that isn’t always the case. Depending on material, machine, fixturing, tool, etc. a standard path may be more productive.
4. Using cheap or poorly maintained tool holders
Holders with poor dimensional accuracy and loose tolerances can damage tools. These subpar holders cause runout, leading to tool failure before they even enter the machine. Using dirty or worn-out holders can also create problems from the start. Failing to clean them between uses can allow chips or other contaminants to weaken the grip strength or TIR of a holder assembly. Always ensure the assembly is disassembled and cleaned between uses to maximize tool life and performance, thereby enhancing productivity.
5. Avoiding spending money on technological advancements
Multi-axis machines, circle segment tools, and new more intuitive CAM software, are just a few example advancements on the front of CNC machining in recent years. “That’s how we’ve always done it” isn’t going to cut it anymore. If the goal is to make money, as mentioned earlier, money needs to be spent (responsibly). Continuous improvements in this industry exist for a reason, and when implemented properly, they can significantly boost productivity and save you money.
Your partners in Productivity
The A&M Industrial Metalworking Team can help you identify the latest innovative Kyocera SGS Precision Cutting Tools for your high performance applications. Contact the A&M Industrial Metalworking Team for expert recommendations that can reduce your cycle times and increase your efficiency.