Aluminum Machining Tips And Techniques
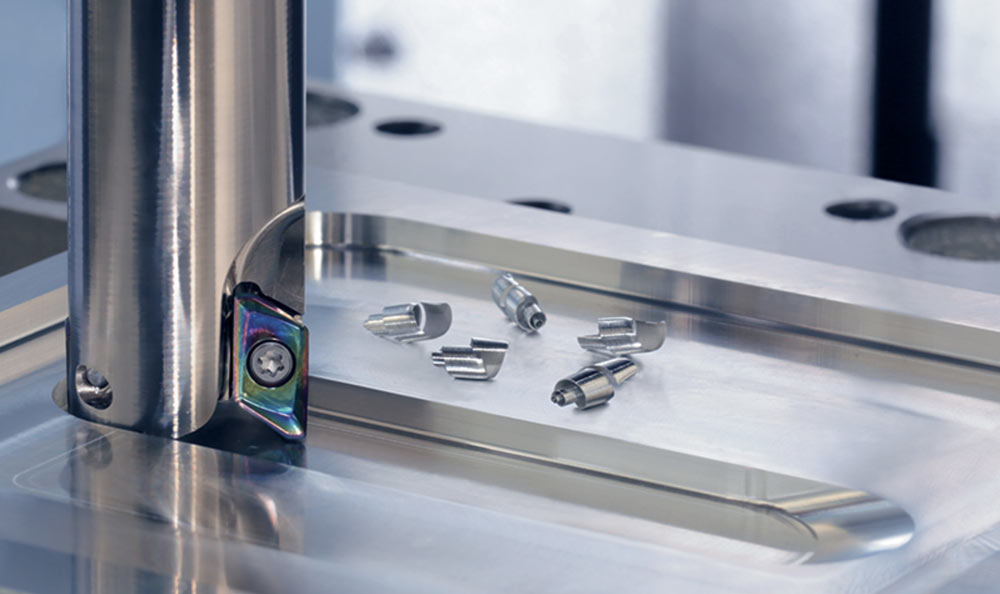
Aluminum is a widely used material in various industries due to its lightweight, excellent strength-to-weight ratio, and corrosion resistance. When it comes to machining aluminum, there are specific considerations and techniques that can help you achieve optimal results. In this blog, we will delve into the art of machining aluminum, providing you with valuable tips and techniques to enhance your machining processes and produce high-quality aluminum components.
Selecting the Right Tooling
Choosing the appropriate tooling is crucial for machining aluminum effectively. Carbide end mills with sharp cutting edges and high helix angles are commonly used for aluminum machining. A helix angle of 35° or 40° is a good choice for roughing and slotting applications. A 45° helix angle is recommended for aluminum finishing applications. High helix end mills offer excellent chip evacuation, reduce heat buildup, and provide longer tool life.
Additionally, consider using coated or specialized aluminum-specific end mills to further enhance performance and reduce friction. Zirconium Nitride (ZrN) coated end mills are recommended for machining aluminum and other non-ferrous materials, as their high hardness and abrasion resistance helps to keep aluminum chips from gumming up and sticking together. Rely on A&M Industrial for a wide range of milling tools and indexable milling tools from trusted brands including Iscar, Micro 100, Kyocera, Nachi, and more.
Proper Machine Setup
To achieve accurate and efficient machining, ensure that your machine is properly set up for aluminum. Rigidity is key, as aluminum tends to generate more vibrations compared to other metals. Reduce chatter by using proper fixtures and workholding techniques. Additionally, check and adjust machine parameters such as spindle speed, feed rates, and depth of cut to optimize performance and minimize tool wear. Refer to manufacturer for speed and feed recommendations when machining aluminum.
Lubrication and Coolant
Aluminum machining can generate heat, leading to chip welding, tool wear, and poor surface finishes. Proper lubrication and coolant application are essential for dissipating heat and improving chip evacuation. Use coolant specifically formulated for aluminum machining to prevent buildup and ensure effective cooling. Flood cooling or through-spindle coolant delivery can be beneficial for efficient heat removal during the machining process.
Consider Chip Management
Aluminum generates long, stringy chips that can cause issues if not managed properly. To avoid chip entanglement, implement techniques such as using chip breakers, and high-pressure coolant to evacuate chips from the cutting surface. Chip management also helps prevent re-cutting of chips, which can negatively impact tool life and surface finish.
Optimize Feeds and Speeds
Finding the right balance of feeds and speeds is crucial for achieving optimal results when machining aluminum. Conservative speeds and feeds can help minimize tool wear and ensure good surface finishes. However, overly conservative parameters can lead to poor productivity. Experiment with different cutting speeds and feed rates to find the optimal balance between tool life, productivity, and surface finish.
Tool Path Strategies
Consider employing proper tool path strategies to maximize machining and metalworking efficiency. High-speed machining techniques, such as trochoidal or adaptive milling, can help reduce cutting forces and heat buildup, resulting in improved tool life and surface finishes. These strategies involve using shorter tool engagement and maintaining constant chip loads, reducing the likelihood of tool chatter and workpiece deflection.
Post-Machining Considerations
After machining, deburring and surface finishing may be necessary to remove sharp edges and give the aluminum workpiece a smooth, professional finish.
Conclusion
Machining aluminum requires attention to detail and employing specific techniques to achieve optimal results. By selecting the right tooling, setting up the machine properly, managing chips effectively, optimizing feeds and speeds, employing suitable tool path strategies, and considering post-machining steps, you can master the art of machining aluminum and metalworking. With these tips and techniques, you can enhance productivity, ensure quality, and unlock the full potential of this versatile metal in your machining operations.
Get free, expert technical support
Contact the A&M Industrial Metalworking Team for additional support selecting the proper tooling for your aluminum machining applications, for recommended speed and feed information, and for machining tips that can help you to reduce cycle times and increase your productivity.