Tube & Pipe Sawing: How To Choose The Best Band Saw Blade For The Job
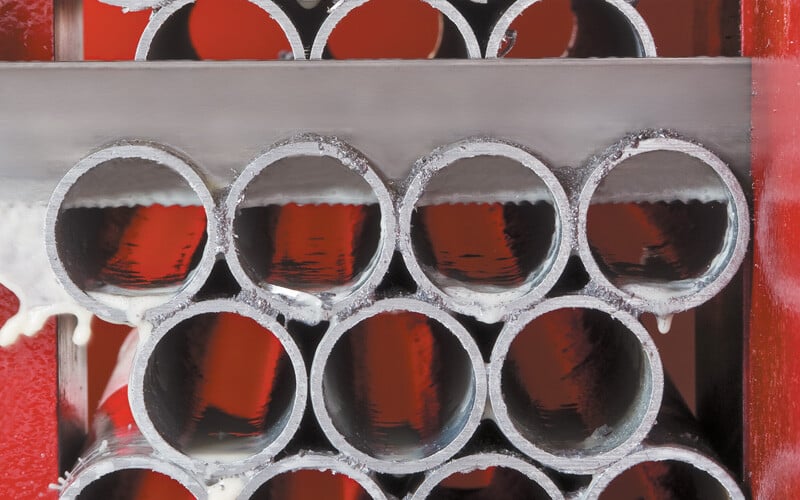
Recognizing common challenges in sawing tubes and pipes can lead to more effective cutting processes. In the following sections, we explore potential issues you might face when cutting bundles, dealing with various materials, addressing scale or straightness problems in tubing, and considering how pipe wall thickness impacts the sawing process.
Cutting Bundles
Cutting bundles of tubes and other structural shapes presents distinct challenges. The speed of cutting bundles depends on the material type rather than the shape, necessitating a different tooth selection.
For instance, when cutting a 4" square pipe with a 1/4" wall, a 4/6, 5/8, or even 6/10 tooth blade might be suitable, depending on the desired outcome. However, when bundling, the cross-section the band saw blade cuts can vary based on the bundle size. Using the 4" square pipe example in a bundle of 4 pieces side-by-side and 4 pieces high, the blade cuts across a 16" solid, depending on the head's angle as it moves through the tops or sides of the tubes. Additionally, the 1/4" wall effectively becomes a 1/2" wall. In this scenario, both 6/10 and 5/8 tooth blades are too fine for efficient cutting, so switching to a 4/6 or even a 3/4 tooth blade would improve cutting rates.
While square tubing is less of a concern, round tubing tends to spin during cutting. Therefore, ensuring that bundles are tightly clamped is crucial. Typically, both side and top clamps are necessary. In some cases, operators may tack weld the ends to prevent spinning, which helps but does not eliminate vibration during cutting. Any vibration or machine chatter can damage the teeth and reduce band saw blade life.
Machine setup is also important when cutting bundles. If the machine head is not canted, determining the correct blade pitch becomes more challenging as the blade "sees" the full material amount. A canted blade will not see the full 16" solid as in the previous example.
Finally, cutting coolant is a key consideration. While flood coolant remains the best for band saw blade life, many mist systems on the market are worth considering. Mist coolants do not flow down the material and pool at the bar ends, but they are less effective, potentially causing heat buildup on the blade. Flood coolant is recommended whenever possible.
Consideration Of Materials
Understanding the material is crucial for selecting the appropriate band saw blade and achieving optimal cutting performance in all sawing applications. Sometimes, identifying the material is straightforward. For instance, distinguishing between a standard A500 tube and an Alloy (4130) steel pipe is visually simple.
However, in other cases, such as with A500 and A53, visual identification becomes more difficult. Despite their similar properties, they require different cutting approaches. Starrett band saw blade speeds are generally determined by the material type rather than its shape. For example, when comparing A500 to 4130, a feed and speed chart can provide a useful starting point. In general, harder materials require slower blade speeds, and this also applies to the feed rate. Harder materials simply do not cut as quickly as softer ones, regardless of their shape or size. Therefore, the feeds and speeds for solid, structural, or tubing materials depend on accurately identifying the specific type of material being cut.
Scale Or Straightness Of Tubing
The material and length of the tube can significantly affect blade longevity, with both scale and straightness being influential factors. A light rust coating from outdoor exposure is generally not problematic, but scale from certain manufacturing processes can be harmful. In some cases, this scale is tougher than the material itself, potentially damaging the blade teeth at the start of a cut. Additionally, when cutting tubes that are 20 feet, 40 feet, or longer, the straightness of the tube impacts the accuracy of the cuts.
Although the pieces are typically clamped, the clamps often lack the strength to fully address the issues posed by crooked pieces. Even if the blade and machine cut straight, a crooked cut can occur if the material is misaligned between the vises. Checking the material with a square after cutting will reveal any inaccuracies. This issue is also prevalent when support tables are not level, causing the material to enter the machine at an angle, resulting in cuts that deviate at either the top or bottom. This can be easily corrected by ensuring the tables are level and making necessary adjustments.
Thin Wall Versus Heavy Wall Pipe
Just like with bundles and all materials, the size and wall thickness of the material dictate the tooth pitch and the type of band saw blades used for different applications. For thinner-walled applications, blades with a sturdier tooth back and a greater set to the teeth are generally preferred. The stronger tooth back offers enhanced strength and better shock resistance for each tooth, resulting in longer blade life as the teeth repeatedly enter and exit the material, moving through both thick and thin sections.
Additionally, these blades often feature a wider tooth set with a larger kerf, which reduces the stress on the material that can cause the blades to pinch. In most situations, a blade with a wider set can completely prevent pinching.
An intriguing aspect of "heavy" wall pipe is that it can sometimes be cut in a manner similar to a solid bar. Depending on what is considered a heavy wall, many of the challenges associated with thin wall pipe are no longer present. Vibrations are minimized, pinching is less severe, and the process of the teeth entering and exiting the material is less problematic because feed rates are generally much slower.
It's important to note that feed rates are determined by the "type" of material and are measured in square inches per minute. Consequently, much heavier walled pipe would cut more slowly from a linear standpoint, as the blade is removing a larger volume of material compared to a thin-walled pipe. In many instances, depending on the definition of thick wall pipe, a band saw blade designed for solid materials can outperform one designed for thin wall and structural materials. A smaller set means a smaller kerf, which results in less material being removed per cut. This leads to faster sawing and more precise control over feed pressure and feed rate.
Efficiency Considerations
To optimize tube and pipe sawing operations, it's crucial to adhere to fundamental guidelines for saw machine and band saw blade setup, along with maintaining good maintenance practices.
- Coolant plays a vital role in both cooling and lubricating. Incorrect mixing or using an inappropriate type of coolant (i.e., one that neither cools nor lubricates) can result in excessive heat and chip welding. Ensuring the correct coolant flow and ratio is essential, as cutting fluid is necessary for almost all materials. It provides both cooling and lubrication to the cutting surface. Without it, excessive heat can lead to reduced band saw blade life and potential tooth stripping.
- Pay attention to the chip brush. If it is worn, misaligned, or missing, replacing or adjusting the chip brush is advisable. Although a chip brush is not directly responsible for chip welding, an improperly installed or non-functional brush can allow chips to accumulate in the gullets, increasing heat and leading to chip welding.
- If the band saw blade teeth appear dull or damaged, replace the blade. Damaged teeth will have altered clearances and angles, resulting in cuts that range from mildly uneven to significantly wavy. Consult our band saw blade troubleshooting guide for more information.
- Loading bundles can be a time-consuming task. When loading material one piece at a time, consider whether it's worth the effort to create a bundle. If numerous cuts are required, bundling is often worthwhile. However, if each piece is only cut a few times, it may be more efficient to cut each piece individually. The decision to bundle cut depends on the number of pieces needing cutting versus the time to create a bundle. Sometimes material arrives pre-bundled, and if all pieces need cutting and the machine can handle the bundle size, it makes sense to load the entire bundle and begin cutting.
- As with any machinery, maintaining the saw is crucial. Before cutting, check guides for wear or cracks, and ensure blade tension and tracking are properly adjusted. Overall, the saw must be in good working condition.
- Since bundles of tubes or pipes are larger than individual pieces, machine issues can be amplified. For instance, if the guides are not correctly adjusted and you're cutting a 4" piece of square tubing, approximately .030 runout may occur. While this might be acceptable for a single piece, stacking four pieces high could result in runout exceeding four times that amount when measured across the entire bundle. This can lead to cuts that fall out of tolerance. Depending on your expectations, bundles can magnify minor issues into problems that produce scrap pieces.
Download Your Free Band Saw Troubleshooting Guide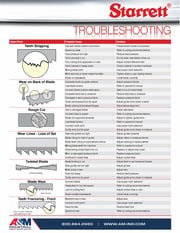
Use the A&M Industrial Starrett Band Saw Troubleshooting Guide to identify the cause and solution to your band saw blade challenges at a glance! Plus, our exclusive guide includes recommended cutting speeds and valuable information on Carbide Tipped Starrett Band Saw Blades. For additional assistance with band sawing, workholding and set-up, aluminum machining, metalworking applications, and more, contact the A&M Industrial Metalworking Team.