Untangling Threading Issues: Tap Troubleshooting Guide
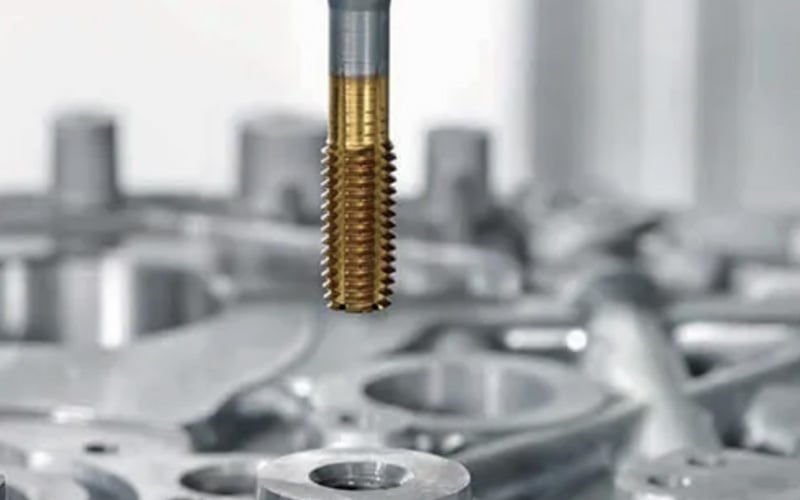
Tapping and threading operations play a crucial role in various industries, including manufacturing, construction, and repair work. However, encountering issues during these processes can lead to frustration, damaged threads, and compromised end results. In this blog, we will explore common tapping and threading issues and provide practical troubleshooting tips to help you overcome these challenges and achieve clean, precise threads.
Broken Taps:
Problem: Broken taps can occur due to excessive force, improper alignment, or workpiece material hardness.
Solution:
- Use appropriate tapping techniques: Apply steady, consistent pressure while tapping and avoid excessive force. Let the tap do the work, and don't try to force it.
- Select the right tap type: Different materials require specific tap types, such as taper, plug, or bottoming taps. Ensure you are using the correct tap for the job.
- Pre-drill and use cutting fluid: For harder materials, pre-drill a hole slightly smaller than the tap diameter and use cutting fluid to reduce friction and ease the tapping process.
Stripped Threads:
Problem: Stripped threads can result from over-tightening, improper alignment, or using the wrong tapping size.
Solution:
- Use the appropriate tap size: Ensure that the tap size matches the screw or bolt being used. Using the wrong size can lead to weak threads and increased chances of stripping. Utilize our free Tap & Drill Size Chart to verify you're using the correct size tap.
- Proper alignment: Align the tap perpendicular to the workpiece to prevent cross-threading. Use a tap handle or tapping guide for more precise alignment.
- Avoid excessive torque: Apply appropriate tightening force when inserting screws or bolts into tapped holes. Over-tightening can lead to stripped threads. Use a torque wrench for accurate control if necessary.
Poor Thread Quality:
Problem: Poor thread quality can result in uneven threads, rough surfaces, or misaligned threads.
Solution:
- Use sharp taps and dies: Dull cutting tools can produce rough threads. Regularly sharpen or replace taps and dies to ensure clean cuts.
- Lubrication: Apply cutting oil or a suitable lubricant during tapping and threading operations to reduce friction and improve thread quality.
- Proper speed and feed rate: Adjust the drilling or tapping speed and feed rate to match the workpiece material. Experiment with different settings to find the optimal combination for smooth, precise threads.
Thread Galling:
Problem: Thread galling occurs when the metal surfaces of threaded parts seize or lock together during tightening, resulting in damaged threads and difficulty in assembly or disassembly.
Solution:
- Use lubrication: Apply an anti-seize compound or a lubricating oil specifically designed for threaded connections to reduce friction and prevent galling.
- Avoid excessive torque: Use a torque wrench to tighten bolts or screws within the recommended torque limits. Excessive torque can increase the likelihood of galling.
- Choose compatible materials: When working with stainless steel, titanium, or other materials prone to galling, select compatible fasteners or use thread inserts to mitigate the issue.
Summary
By implementing effective troubleshooting techniques, including employing correct tapping techniques, selecting the appropriate tap size, applying lubrication, and avoiding excessive force or torque, you can significantly diminish the occurrence of broken taps, stripped threads, poor thread quality, and thread galling. It is crucial to carefully choose the right tools, consider the workpiece material, and practice patience and precision. For further assistance overcoming metalworking and machining challenges, contact the A&M Industrial Metalworking Team. A&M Industrial carries a wide variety of taps from trusted brands including Nachi, Morse Cutting Tools, YG-1 and more, to ensure we have the right tap for your threading application.