Exploring the Differences Between Abrasive Wheels
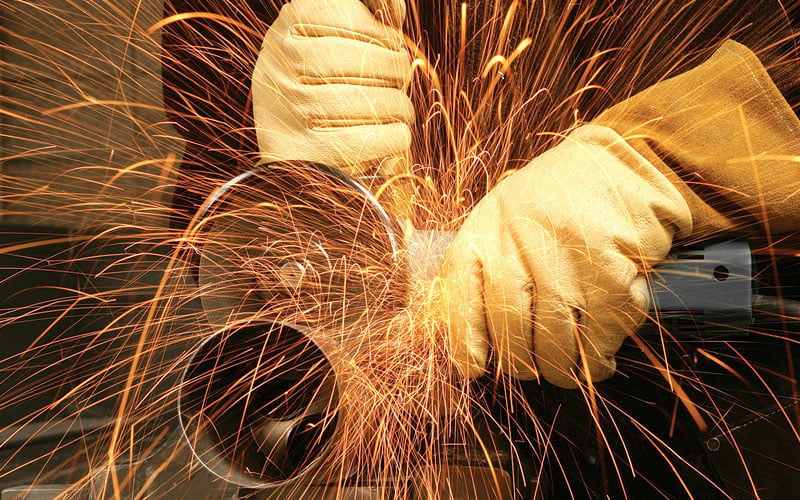
Abrasive wheels are essential tools used in various industries for cutting, grinding, and finishing applications. These wheels come in different types, each designed for specific materials and tasks. Understanding the differences between abrasive wheels is crucial for selecting the right abrasives to achieve optimal performance, efficiency, and safety. In this blog, we will delve into the various types of abrasive wheels, their unique characteristics, and their ideal machining and finishing applications.
Grinding Wheels
Grinding wheels are among the most common abrasive wheels, widely used for stock removal, surface finishing, and sharpening operations. They consist of abrasive particles bonded together by various materials such as vitrified bonds, resin bonds, or metal bonds.
- Composition: Grinding wheels can be made with various abrasive materials, including aluminum oxide, silicon carbide, and diamond. Aluminum oxide wheels are versatile and suitable for general-purpose grinding, while silicon carbide wheels are ideal for grinding non-ferrous materials. Diamond wheels are the hardest and used for grinding hard materials like carbides and ceramics.
- Applications: Grinding wheels are employed in industries such as metalworking, woodworking, and fabrication for tasks like shaping, smoothing, and removing excess material from workpieces.
Cutting Wheels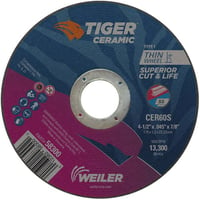
Cutting wheels, also known as cut-off wheels or abrasive discs, are primarily used for cutting through metal, masonry, and other hard materials. Cut-off wheels feature a thin profile and are reinforced with fiberglass mesh or resin to enhance strength and stability.
- Composition: Cutting wheels typically consist of abrasive grains (aluminum oxide or silicon carbide) bonded with resin or a combination of resin and fiberglass reinforcement.
- Applications: Cutting wheels are extensively used in metalworking, construction, and maintenance applications to cut through pipes, rods, bolts, and other solid materials. See our blog on the best abrasives for stainless steel and the best abrasives for aluminum for additional application support.
Flap Wheels
Flap wheels, also known as flap brushes, are versatile abrasive wheels that combine both grinding and finishing capabilities. They consist of overlapping abrasive flaps mounted on a spindle or hub, allowing for continuous contact with the workpiece.
- Composition: The abrasive flaps on flap wheels are made of various materials, such as aluminum oxide, zirconia alumina, or ceramic grains, coated on a flexible backing material like cloth or paper.
- Applications: Flap wheels are commonly used for blending, deburring, and finishing operations on metal surfaces, including welds, edges, and contours.
wheel Brushes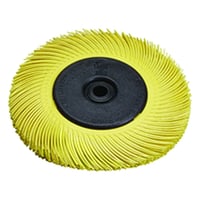
Wheel brushes are abrasive tools used for cleaning, deburring, and surface preparation. They consist of metallic wires or bristles mounted on a rotating spindle or brush holder.
- Composition: Wheel brushes are available in different wire materials, including steel, stainless steel, and brass, each offering specific properties suited for different applications.
- Applications: Wheel brushes are employed in industries such as metalworking, automotive, and maintenance for tasks like rust removal, paint stripping, and surface cleaning.
Summary:
Abrasive wheels come in a variety of types, each tailored to specific tasks and materials. Understanding the differences between grinding wheels, cutting wheels, flap wheels, and wheel brushes is essential for selecting the right tool for the job at hand. Whether you need to shape, cut, grind, or finish a workpiece, choosing the appropriate abrasive wheel ensures optimal performance, efficiency, and safety in your operations. Remember to consider factors such as wheel composition, grit size, and compatibility with the workpiece material. By leveraging the strengths of various abrasive wheels, you can achieve exceptional results in your cutting, grinding, and finishing applications.
Need help selecting an abrasive wheel?
We can help you determine the right abrasive wheel for your application and material. Contact the A&M Industrial Metalworking Team to request assistance.