How To Reduce Scrap In Manufacturing
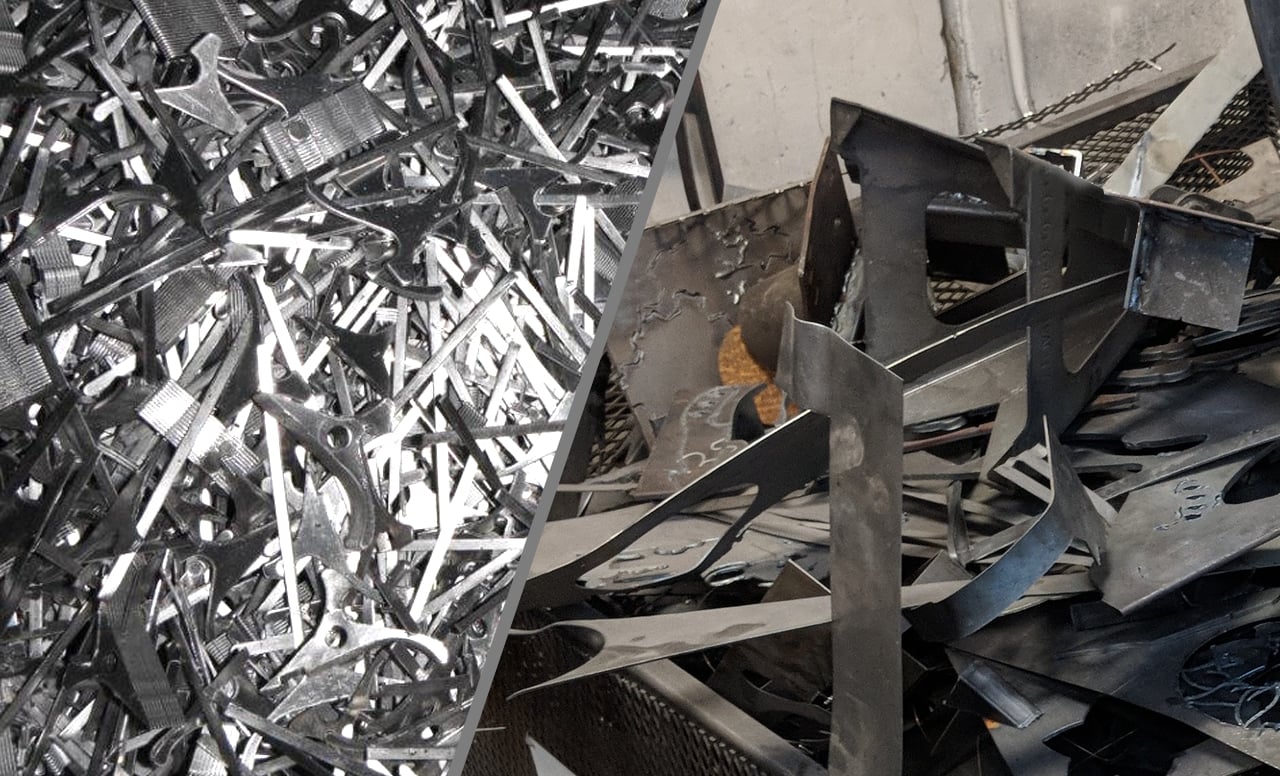
We're diving into a topic that's close to the hearts of many machine shop owners and manufacturers – reducing scrap and waste. Not only can minimizing waste help you save money and resources, but it also contributes to a cleaner and greener work environment. So, let's roll up our sleeves and explore some practical tips on streamlining your machine shop operations.
Optimize Material Usage:
Every piece of wasted material is like a tiny dagger to your bottom line. To tackle this issue head-on, start by carefully planning and measuring your materials before starting any project. By optimizing your material usage, you can minimize the amount of scrap generated. Consider using nesting software to maximize the utilization of sheet metal and minimize waste during cutting operations. Contact the A&M Metalworking Team for assistance with planning for a job or for help identifying how much material an application will require.
Streamline Your Workflows: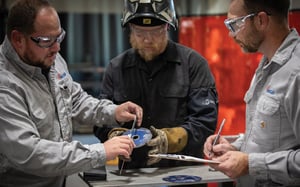
Efficient workflows are the backbone of any successful machine shop. Take a closer look at your production processes to identify bottlenecks, redundancies, or inefficient practices. Are there any unnecessary steps in your machining operations? Can you consolidate tasks or streamline the flow of materials to reduce handling and minimize waste? By identifying and addressing these areas, you can optimize your operations and reduce scrap. Request a free abrasives assessment or request a machining fluids assessment for an in-depth review and streamlining of your shop's current workflows and practices by our metalworking experts and vendor partners.
Embrace 5S & Lean Manufacturing Principles:
Lean manufacturing is all about eliminating waste and maximizing value. By implementing lean principles in your machine shop, you can tackle scrap and waste head-on. Consider adopting practices such as 5S (Sort, Set in Order, Shine, Standardize, Sustain) to organize your workspace and reduce clutter. Implementing visual management techniques, like shadowboards, allows tools and equipment be readily located, minimizing inefficiency.
Perform Regular Equipment Maintenance:
Neglected machinery can lead to increased scrap and waste due to inaccurate cuts, poor tolerances, and overall decreased productivity. Regular equipment maintenance is essential to keep your machines running smoothly and producing high-quality parts. Create a maintenance schedule, perform routine inspections, monitor your metalworking fluids, and address any issues promptly to avoid scrapping parts due to equipment-related failures.
Invest in Training and Skill Development:
A well-trained workforce is more likely to produce accurate results, leading to less scrap and waste. Invest in training programs and workshops to enhance the skills and knowledge of your machine operators. Encourage open communication and information sharing within your team to foster a culture of continuous improvement. A knowledgeable and motivated team will be better equipped to identify and address potential waste-generating issues. Contact the A&M Metalworking Team for information on training opportunities we can provide.
Conclusion:
Reducing scrap and waste in your machine shop not only saves you money but also helps create a more sustainable and efficient operation. By implementing these tips and embracing a lean mindset, you can streamline your workflows, optimize material usage, and maintain high-quality standards. Remember, it's an ongoing process, so stay vigilant and continuously seek opportunities for improvement.